GMP车间
2025-2-28
一、科学布局设计,构建洁净生产核心
- 分区规划与洁净度分级
GMP车间需按生产工艺划分A、B、C、D四个洁净级别(A级为高风险操作区,B级为背景区,C/D级为辅助区),并严格分离人流、物流通道,避免交叉污染。原料存储、生产操作、包装等区域需通过物理隔离或缓冲区衔接,确保动态与静态环境均符合《中国GMP(2010)》及ISO 14644标准。 - 材料与结构优化
采用彩钢板隔断、环氧自流坪地面及防静电涂层,确保墙面无死角、地面易清洁。洁净室层高需满足设备安装需求(如层流罩、隔离器),同时预留维护通道,推荐高度≥2.6m。
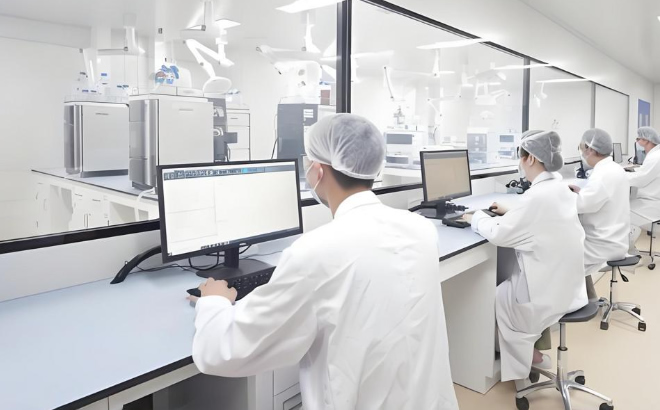
GMP车间
二、空气净化系统:精准控制洁净环境
- 层流与乱流复合设计
- A/B级区:采用垂直层流系统(风速0.36-0.54m/s),配合高效过滤器(HEPA/ULPA)保障局部超洁净环境。
- C/D级区:结合乱流式送风,通过空调箱与末端高效过滤实现动态压差控制,降低能耗。
- 温湿度与压差管理:温度18-28℃,湿度45-65%;相邻区域压差≥10Pa,通过智能传感器实时监控。
- 除尘与排风系统
针对粉碎、制粒等高产尘工序,设计局部排风罩+集中除尘系统,并通过转轮式换热器回收能量,减少新风负荷。
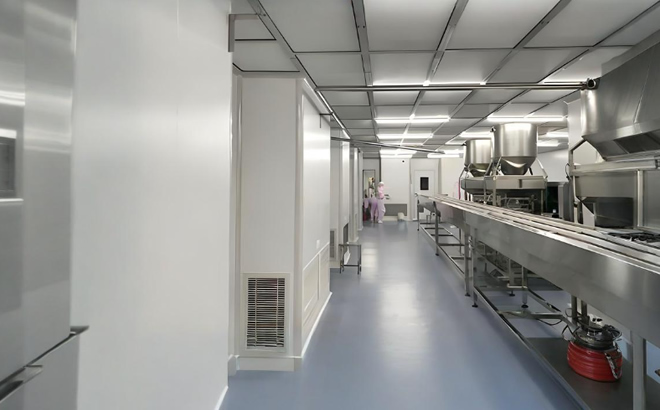
GMP车间
三、设备选型与智能化管理
- 合规设备配置
选用通过GMP验证的自动化生产设备(如一步制粒机、隔离灌装线),表面采用316L不锈钢材质,便于在线清洗(CIP)及灭菌(SIP)。 - 数字化监控平台
集成EMS(环境监控系统)与SCADA(数据采集系统),实时监测尘埃粒子、浮游菌、温湿度等参数,数据存储可追溯,支持远程报警与报表生成。
四、施工与验证:全周期质量保障
- 模块化施工与验收
采用BIM技术模拟施工流程,分阶段进行DQ(设计确认)、IQ(安装确认)、OQ(运行确认)及PQ(性能确认),确保洁净室动态测试达标。 - 人员与文件管理
建立三级培训体系(GMP法规、操作技能、应急预案),配套SOP文件库及电子批记录系统,实现变更控制与审计追踪。
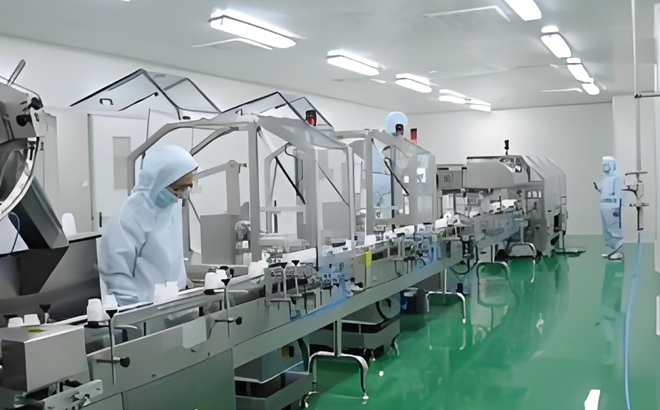
GMP车间
五、案例应用与后期维护
- 典型场景优化
- 口服固体制剂车间:合并制粒、干燥等前段工序,设置独立除尘单元,提升设备利用率。
- 无菌灌装线:采用RABS(限制进出屏障系统)隔离核心操作区,降低人员干预风险。
- 运维服务
提供年度洁净度检测、过滤器更换及系统升级服务,延长车间生命周期,降低合规风险。
THE END